
Outside a warehouse in a Los Angeles suburb, there’s a fascinating experiment underway in how people can live in places at high risk of flooding. A prototype of a new type of housing has been undergoing tests in a large tank of water. The homes, made from a kit of plastic parts, are designed for flood zones: The foundation and the watertight shell of the house can float. When the water rises, the house rises, too.
“Normally, it just sits on land,” says Charles Wee, the architect behind the design. “And then during a flood, it can actually just rise in the same position.”
Wee spent most of his career working on conventional high-rise projects. But a decade ago, after visiting a relative who worked with indigenous communities in the Amazon, he decided to change direction. He’d seen how people living along the Amazon River lost their homes—simple shacks on stilts—every time the river flooded. Globally, more than a billion people face a significant risk of flooding, and that number is growing. Wee began considering how to build housing in flood plains differently.
Learning from a disaster
At first, Wee wasn’t sure how to approach the idea of making a buoyant home. But he happened to see a photo taken after the 2011 earthquake and tsunami in Japan. The image showed wreckage from destroyed buildings filling the coastline.
Wee noticed large blue boxes floating intact in the water. He discovered that they were molded tanks used by the fishing industry. They were cheap to produce and seamless, so water couldn’t intrude. He realized that he could use the same low-cost manufacturing technique to make building parts.
Wee closed his own lucrative architecture practice and founded a startup, LifeArk, to work on the new concept. The development was challenging. He wanted to make homes that would not only be resilient in floods, but that could withstand other disasters, including earthquakes, hurricanes, and wildfires.
After years of R&D, his team had a system that worked. It also meets the requirements of the California building code, one of the most restrictive building codes in the world. In its factory in California’s Central Valley, the company now makes prefab housing parts using rotational molding, the process uses to make other hollow plastic products like coolers or playground equipment. Inside a large machine, a plastic-filled mold rotates, producing seamless roofs, doors, columns, and other parts. The shell is high-density polyethylene (HDPE), the same plastic used in products like milk jugs and shampoo bottles. It’s filled with foam insulation that makes it energy efficient, strong, and buoyant.
A better use for plastic
Most plastic is used “in the worst possible way,” Wee says. But one of plastic’s environmental flaws—the fact that it doesn’t easily break down—can be an advantage in a building. “Plastic will last 100 years without degradation,” he says. “It’s a great material to build homes, but we use it to make shopping bags.”
LifeArk’s homes, which are the first to use plastic as a load-bearing material, can last longer than modular homes made from more typical building materials. At the end of a home’s life, the manufacturer can fully recycle the plastic. (The company also uses around 30% postconsumer recycled material.)
Plastic makes the homes resilient in earthquakes. In seismic testing on “shake tables,” the material was flexible enough that it bent but never broke. Similarly, in a hurricane, the buildings can bend in strong winds. Making the homes resilient to fires was a bigger challenge, since plastic easily melts. But the team developed a compound that’s mixed into the plastic that makes it carbonize in the event of a fire, forming a layer of black soot so the fire can’t penetrate and it self-extinguishes.
The Lego-like parts can be assembled into simple 8-by-8-foot modules without equipment. Then those modules can be laid out into homes. In one version of the housing, with a floating foundation and piers, the homes can adjust to floods or float permanently on water. (One proposal from the company looked at how the design could be used for ocean-based housing in the Marshall Islands to help deal with sea level rise.) In another version, the modules sit on a foundation that’s raised 28 inches above the ground.
The company has already built multiple projects, with others underway. But so far, the first developments haven’t yet used the amphibious version. Because the concept is new, it isn’t yet possible to insure. It also needs to overcome regulatory barriers. The first projects use a more standard foundation, though they also have advantages in flood zones.
A new solution for supportive housing
In a project in Watsonville, California, the design makes it possible to build in a flood zone. When a nonprofit in the small city wanted to build housing for people experiencing homelessness in a church parking lot, they initially planned to use another type of modular housing. But it would have cost $1 million to raise the other homes above the flood level. Because LifeArk’s homes are already raised off the ground, it was far less expensive to make the housing high enough to avoid an extreme flood.
The company also used the design in other supportive housing projects. In West L.A., one project that just opened on a city-owned parking lot includes 33 bedrooms and bathrooms around a central courtyard. Another project that opened last year, in an L.A. suburb, has 25 units for short-term stays for people experiencing homelessness.
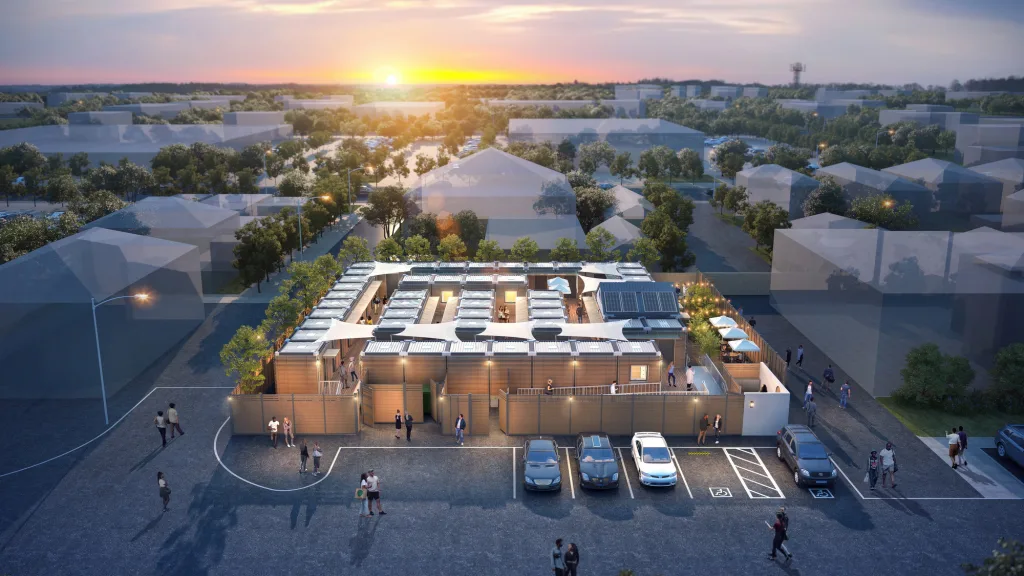
For supportive housing like this, the design can help significantly reduce costs. It’s faster to build than other modular housing, with less labor required. The raised design also allows contractors to install utilities under the homes, rather than in trenches underground that are expensive to build. The company’s first project, in another L.A. suburb, demonstrated the advantages.
“At the time, California was spending a minimum of half a million dollars a unit for housing,” Wee says. “That was our first project, and so we made a lot of mistakes. But we still came up at least two to three times faster and at least half the cost.”
As production scales up, the cost could come down further, making it more viable for use in disasters and in developing countries. And as the company builds more supportive housing projects, it’s still working to make the amphibious version of the housing a reality.
“There’s ample evidence that it will be far more economical in the long term to build an amphibious house in flood-prone zones than to repair homes damaged by floods,” says Wee. “I am a strong believer that if we can crack this nut—mostly regulatory and insurance—this could open up whole new housing opportunities.”